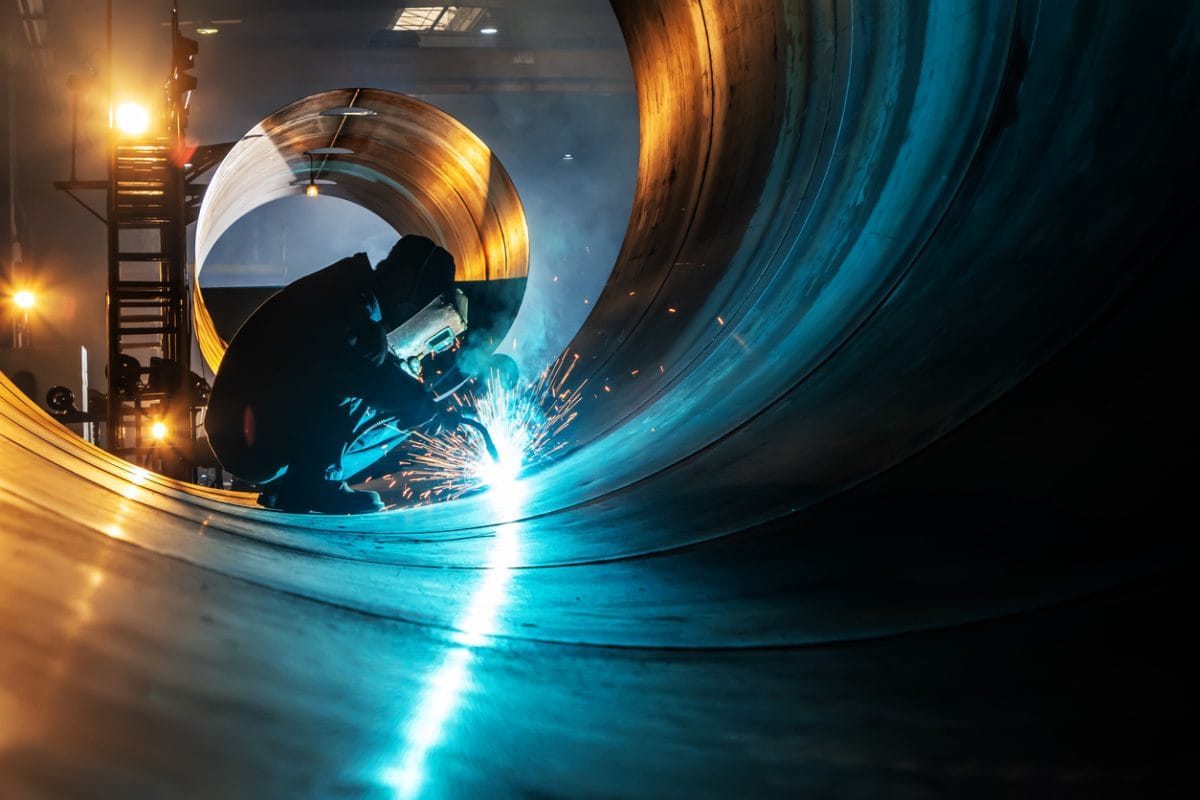
Decarbonising steel: Can the industry go ‘green’?
Steel’s great decarbonisation challenge
Modern life can’t function without steel.
It’s everywhere, from the high-rise buildings in which we live and work to the cars we drive, the planes we fly, the ships we sail to the wind turbines that increasingly provide us with energy.
Our world is built on steel, and it has a crucial role to play in enabling the transition to Net Zero.
However, as with so many of the critical materials in the clean energy transition, the industry has its own daunting decarbonisation challenge, one of the greatest facing the ‘hard to abate’ sectors.
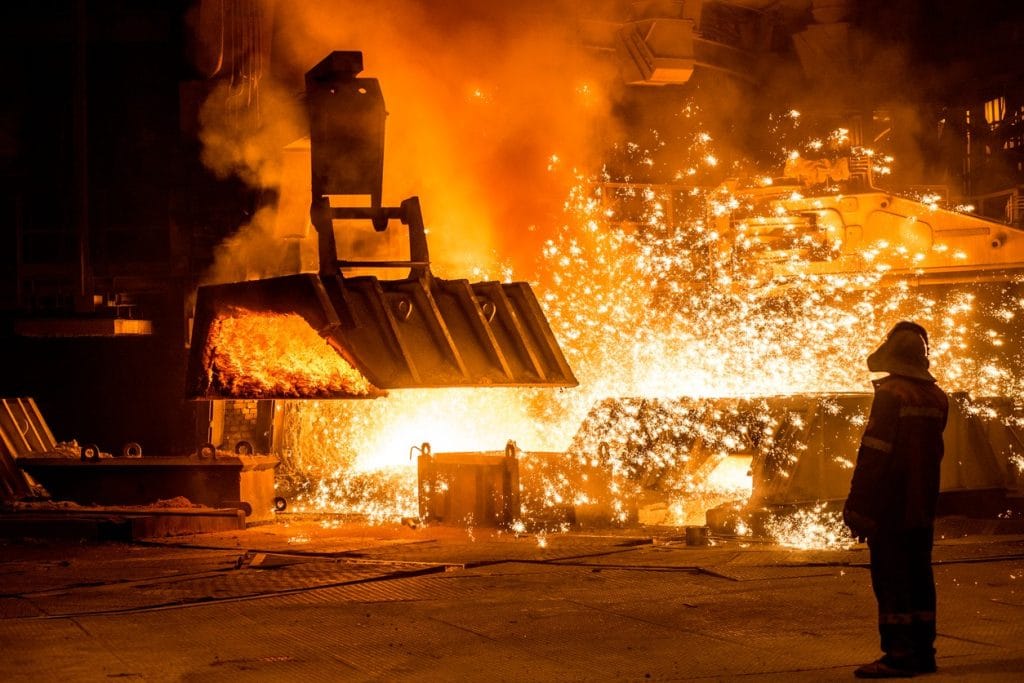
The growing demand for steel
The steel industry now produces close to two billion tonnes of crude steel every year, and that number is trending up. The increasing demand comes from population and economic growth, particularly in India, China, the rest of Asia, and Africa. Steel is also used in wind turbines, electric vehicles (EVs), and other manufacturing related to the decarbonisation industry.
However, steel’s dilemma is that it’s also the largest greenhouse gas (GHG) emitter of all the manufacturing sectors, accounting for around 7% of global emissions.
70% of total global steel production still relies directly on coal as a key raw material and fuel. It’s one of the last sectors that the International Energy Agency (IEA) predicts will still be using coal in 2050 in its Net Zero pathway.
For context, it takes around 770kg of metallurgical coal or met coal to make the steel used in a typical mid-sized car. The industry used 1.1 billion tonnes of met coal in 2021 to produce 1.95 billion tonnes of crude steel, and steelmakers emit between 1.4-1.8 tonnes of CO2 per tonne of crude steel.
Everyone agrees that reducing the industry’s GHG emissions is a real priority. How we reach that goal is another matter because the transition to decarbonised steel comes with a high cost.
Steel’s dilemma is that it’s also the largest greenhouse gas (GHG) emitter of all the manufacturing sectors, accounting for around 7% of global emissions.
Existing ageing infrastructure means that many producers are facing urgent investment decisions now: 71% of blast furnaces will need major refurbishment before 2030, according to the International Renewable Energy Agency (IRENA). That means manufacturers must either go all-in to decarbonise, which will require significant capital investment, or they can overhaul their blast furnaces and risk them becoming ‘stranded assets’ if the market prioritises decarbonised steel over conventional, emissions-intensive steel products.
Current price signals aren’t attractive enough to build enough momentum behind the transition to ‘green’ steel. Last year, ArcelorMittal, the world’s second-largest producer, said that plans to decarbonise the industry would raise steel prices by 10-20%, making decarbonisation much more challenging in the near term.
However, according to Kajsa Ryttberg-Wallgren, head of hydrogen at H2 Green Steel, a Swedish start-up which runs a ‘green’ steel plant in Northern Sweden, the tide is already turning and “there’s growing appetite for customers to pay the ‘green’ steel premium to meet their ESG commitments.”
Eventually, the prospect of facing regulatory penalties, reputational risk and an inability to compete as ‘green’ steel’s market share increases may take the decision out of the manufacturer’s hands.
- How close is so-called ‘green steel’ to being a tangible reality?
- What does the pathway to decarbonising steel look like?
- And how is the industry responding?
That’s the focus of this edition of ‘The Commodity Perspective’.
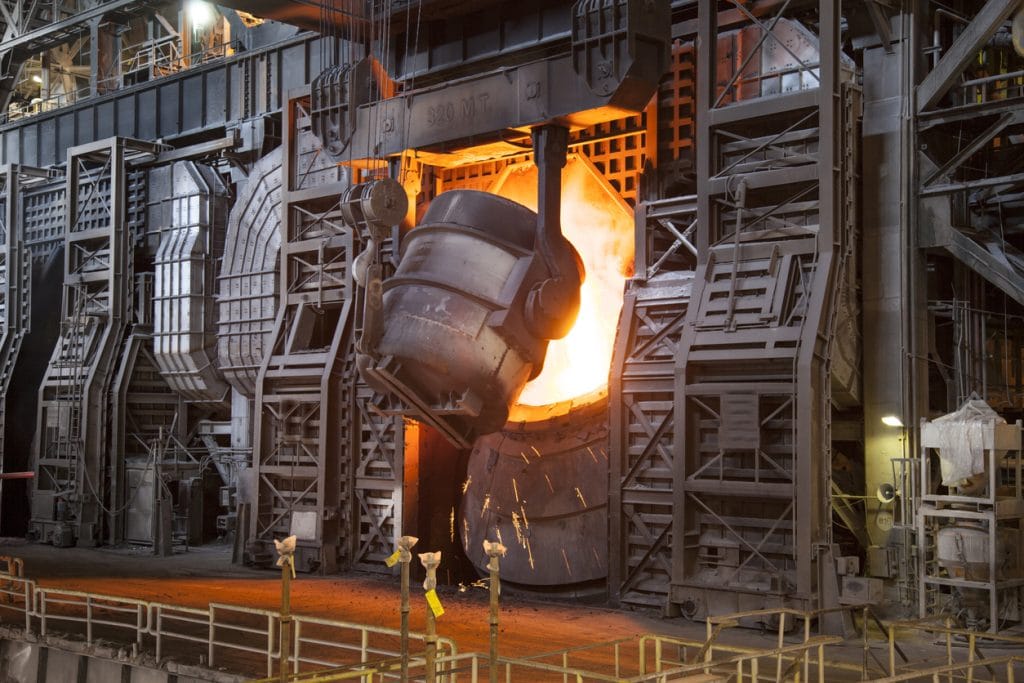
The steel-making process
Steel is made from iron ore, which, once mined, is transformed into steel using two different processes: the blast furnace/basic oxygen furnace (BF/BOF) route and the electric arc furnace (EAF) route.
Primary steelmaking consists of two steps. The first involves reducing iron ore into pure iron, which is then turned into steel. This process requires very high temperatures and significant energy input.
Blast furnace/basic oxygen furnace (BF/BOF)
In the BG/BOF process, blast furnaces produce iron from iron ore. In the second step, a basic oxygen furnace turns iron, with some scrap steel added, into steel. Met coal is used as a feedstock to reduce the iron ore and as an energy source to generate heat in the furnace.
Electric arc furnace (EAF)
The EAF process works primarily by melting scrap steel using a powerful electric arc generated between electrodes and the raw materials. The ambition is for that electricity to be fully renewable eventually.
Although EAF primarily uses recycled steel as a feedstock, it can also be used to produce primary steel using ‘direct reduced Iron’ (DRI). DRI is iron ore that’s been reduced by a gas, most commonly natural gas, but can also be hydrogen.
Which is where the potential for ‘green’ hydrogen comes in.
The commodities in the steelmaking process are some of the most important globally in terms of production, consumption and transportation. The steel industry used 2.3 billion tonnes of iron ore in 2021, making it the third largest commodity in terms of production volume – after crude oil and coal – and the second most traded commodity – after crude oil. Ferrous scrap is the world’s largest commodity in terms of recycling activity.
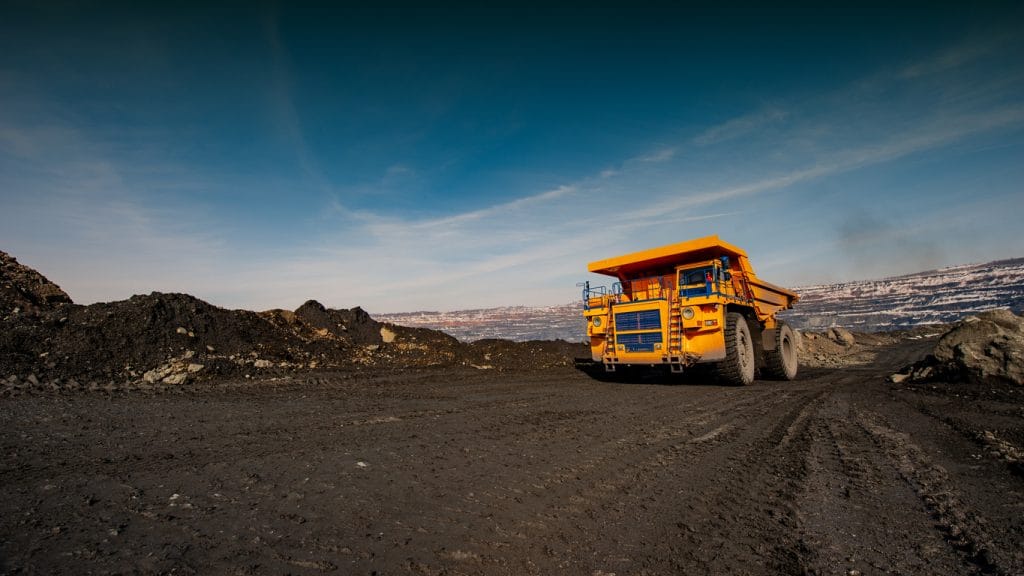
What is ‘green’ steel?
It’s a good question and one without a universally agreed answer!
Generally, when we talk about ‘green’ steel, we’re referring to steel that has been produced with much lower carbon emissions than conventional processes. The ambition is that it will mean steelmaking without the use of fossil fuels in the future.
The current best pathway to that involves electrification from renewables and using ‘green’ hydrogen as a reducing agent to replace coal.
Carbon capture and storage (CCS) is also emerging as a potential pathway, but the technology has yet to prove commercially viable, and there are still relatively few CCS operations globally. CCS technology would also still mean using coal in the production process to make primary steel in many cases.
You can read more about ‘green’ hydrogen in this edition of ‘The Commodity Perspective’.
We’re facing a critical moment for ‘green’ steel.
The steel industry is significantly behind its goal of reaching Net Zero by 2050. According to the NGO Global Energy Monitor, some of its most promising pathways, including electric arc furnaces, have stagnated. Currently, the volume of global steel produced via the EAF pathway is around 30%, but much of that capacity doesn’t yet use renewable energy.
Carbon-neutral steel is certainly possible, but there are prohibitive cost implications. The optimal solution for decarbonisation would be to use ‘green’ hydrogen-reduced’ direct-reduced Iron’ (DRI) in EAFs using renewable energy. However, that process is still years away from scaling. The challenge for many of these ‘hard to abate’ industries is that there isn’t enough green energy or green hydrogen to go around.
As with many of the other clean energy sectors we’ve covered over the last year in ‘The Commodity Perspective’, offtake agreements are key to enabling ‘green’ steel’s momentum. Bloomberg NEF estimates that ‘green’ steel is currently trading at a 40% premium to conventional steel, which means that only higher margin industries like the automotive sector can afford to make the long-term offtake agreements that ‘green’ steel needs to grow. Until premiums lower, it’s still too expensive for low-margin but high-steel-consuming industries like construction.
This means that the steel industry is at a crossroads. Stakeholders know the path forward but are in a relative holding pattern, waiting for other key parts of the clean energy transition to become commercially viable or for a meaningful reduction in the ‘green’ steel premium to tip the balance.
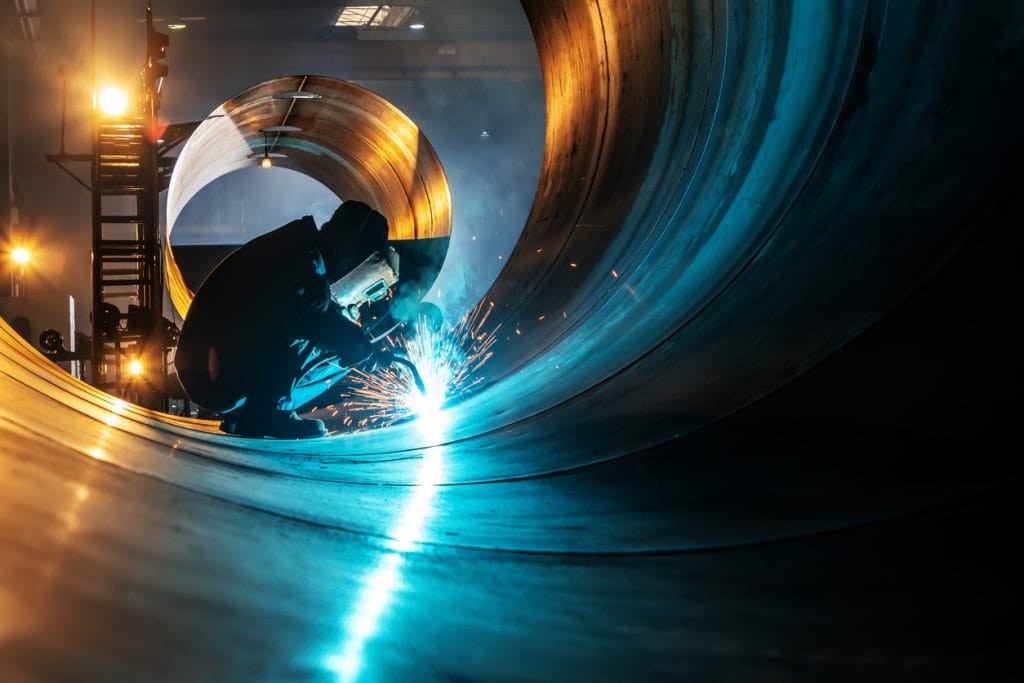
How is the industry responding?
Despite the challenges, the largest steelmakers are responding. In China, where the country’s steel mills produce the majority of global steel and about 15% of China’s total GHG emissions, the government is pursuing ambitious ‘Dual Carbon’ goals of peaking its carbon emissions by 2030 and reaching carbon neutrality by 2060.
Decarbonising its iron and steel industries is a major part of that roadmap. China’s state-owned steelmaker Baowu is by far the world’s largest producer, and it says it’s making promising progress in developing new furnaces that greatly reduce carbon emissions using hydrogen.
Chinese steelmakers are also innovating using hydrogen in the DRI process, but most of that gas is still from non-renewable sources.
India, the world’s second-largest steel producer after China, has said it’s committed to lowering emissions from the iron and steel industry by 2030. However, it has yet to publish a full roadmap for its steelmaking industry, which still relies heavily on the most polluting production processes.
It may eventually be international policymakers that accelerate decarbonisation efforts in both countries. The EU’s Carbon Border Adjustment Mechanism (CBAM) is due to come in by 2026 and it will act as a carbon tariff on steel imports to the EU. As the bloc is the largest importer of steel globally, it will naturally reduce the competitiveness of Indian and Chinese steel unless they lower their carbon footprint.
Steelmakers in the EU have been leading the way in decarbonisation efforts. Not just Swedish companies like H2 Green Steel but also in Germany, which has one of the most advanced renewables economies globally. There, the steelmaker Salzgitter AG has announced that it will start converting to green hydrogen-based steel production by 2026.
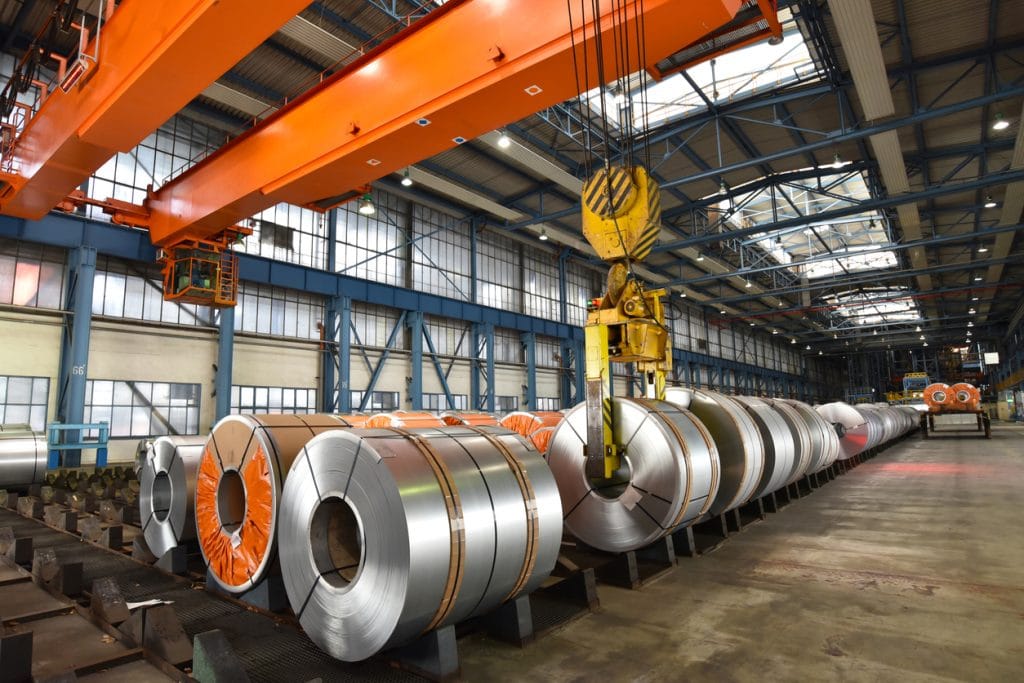
Transforming the steel industry
Globally, research and development projects are focused on transforming the steel industry’s carbon emissions. However, as we’ve highlighted, there are still many obstacles to this transformation. The traditional steel industry is built on fossil fuels and carbon emissions; mills are often located in areas where renewable energy is scarce, and the infrastructure involves significant capital investment. Greater vertical integration could be one solution, with steelmakers investing in green hydrogen or renewable projects to ensure supply.
The journey towards ‘green’ steel is a complex and multifaceted challenge, but it is not insurmountable.
The transition to ‘green’ steel relies on a combination of technological innovation, financial investment, policy support, and market dynamics. The development and scaling of technologies like green hydrogen-based DRI and renewable-powered EAFs are critical.
The traditional steel industry is built on fossil fuels and carbon emissions
Policy frameworks and international agreements will play a crucial role in accelerating this transition. Additionally, customer awareness and demand for sustainable steel products will shift market preferences towards green steel, despite its current premium.
The goal of a fully decarbonised steel industry is ambitious, but despite the challenges, it mustn’t feel out of reach. The sector has to keep pushing forward and innovating because, in reality, there is no second chance.